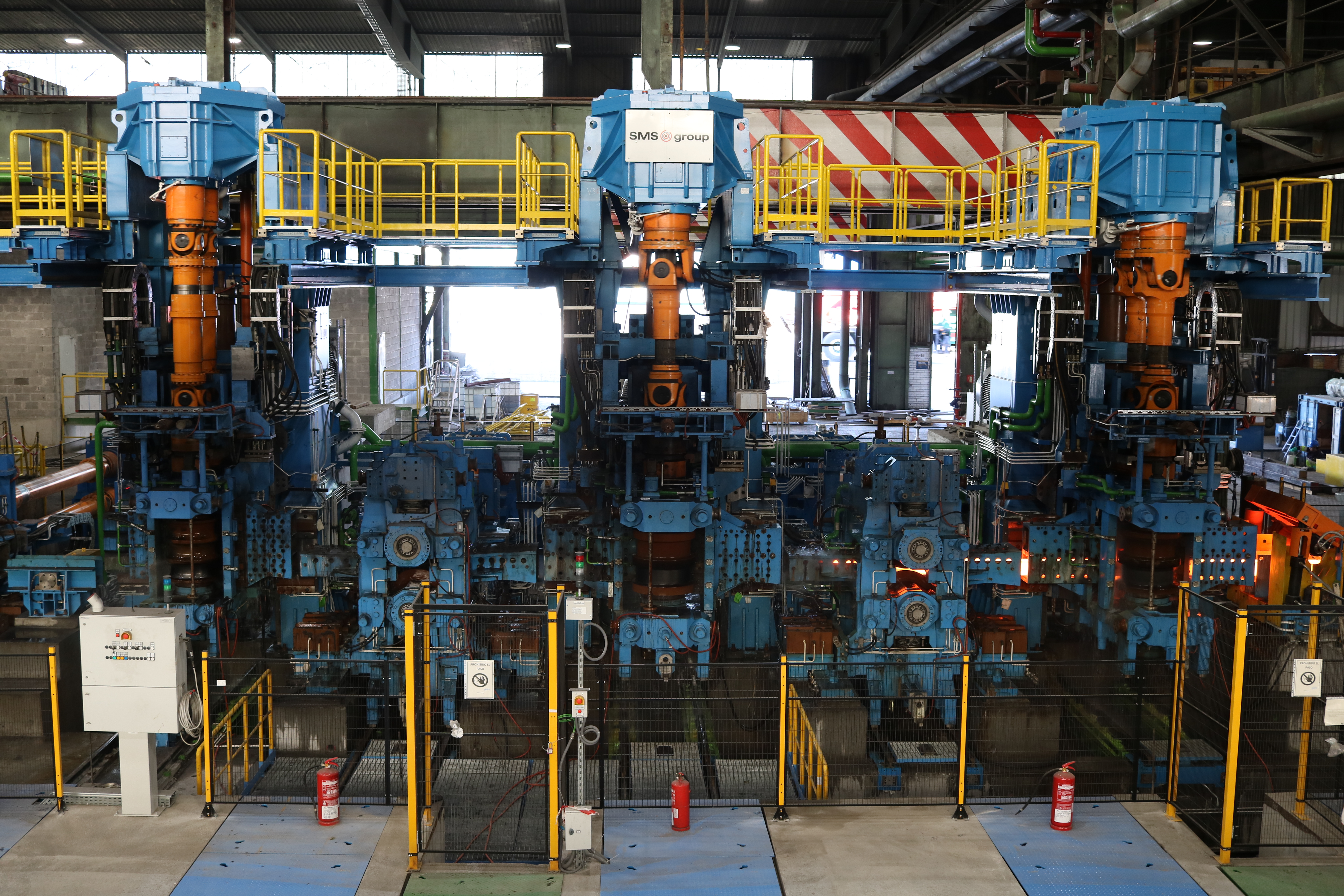
Although the European Union is the second biggest steel producer worldwide, it has been facing various threats for years: a major loss in production capacity compared with the rest of the world and, above all, with China, the need to be more and more cost competitive in order to ensure the viability of the car production line as well as the European metal mechanical industry and, finally, the need to somehow offset the cost increases generated by higher European environmental and energy requirements.
In order to face this complex situation, Sidenor Aceros Especiales S.L., as a European leader in special steel long products, has decided to carry out a project aiming at developing new high added-value products, based on a wide manufacturing spectrum of rolled bars of high surface and internal quality.
The achievement of this ambitious project has been possible thanks to the renovation of the rolling mill at the plant of Basauri, which now has a new and more efficient reheating furnace and a mill that is adapted to a bigger billet.
An essential part of Sidenor’s bet consists in increasing the geometrical dimensions of the continuous casting billet up to a square format of 240mm (compared to the current 185mm). This will increase the final reduction which is applied to the material during the rolling process, and significantly improve the quality of the surface as well as the internal quality of the rolled product.
Regarding the reheating furnace, the new installation is based on the technology of walking beams, which enables a more homogenised distribution of temperature inside the furnace and, thus, the optimization of the heating curves, for improved quality as well as a more efficient use of energy.
The adaptation of the 240-billet rolling mill has required the installation of a new continuous grinding in the shape of 6 H&V boxes, where an average reduction of 20% can be obtained. 2 new (H&V) boxes were thus added to the mill in order to process the grounded material with improved tolerances, apart from other auxiliary elements which contribute to a high-quality product. Once more, energy efficiency is the essential element in the rolling mill, as it has been designed so as to reduce losses of temperature between head and tail and along the mil.
The new rolling mill uses the market leader technology and serves as a basis for the “innobars by Sidenor” concept. The application of the knowledge gained from Sidenor R&D’s more than 30 years of experience in the development of sustainable products and processes, manufacture in cutting-edge installations as well as the use of the latest possibilities of Industry 4.0 complete the pillars of this label and meet the most demanding requirements and value expectations of our clients. This is of high importance in the car industry, which is currently facing the challenge of developing more and more complex components, with better services and at a lower cost. This market represents 70% of Sidenor’s production.